Recently we’ve worked on several projects to re-create hard-to-get classic car parts, exact-fit custom parts for restorations, and custom adapters.
The first featured part that we designed was a custom fit cluster plate for the center dash/console for a 60’s era resto-mod Camaro project. The owner had two new gauges they wanted to mount where the radio fit, so they provided pictures, measurements of the dash opening, the gauges themselves, and a hand sketch to give us an starting point for their desired solution. We iterated several times with various prototype solutions to do test fits, got feedback, and adjusted the angles of the two gauges to the customer’s desires.

Our second project was to adapt a MK6 VW emblem to the trunk lid of a MK5 VW. The newer VW emblem has a subtle body curve to the mounting surface while the inset badge mounting location on the car is flat. We carefully measured, calculated, and designed a slim adapter plate that fit both the car surface on one side and the curve on the back of the badge perfectly. Some carefully-applied 3M emblem adhesive strips on both sides on both sides of the adapter firmly attached the emblem. A jig was designed to fit in and center on the inset location on the car to assure the emblem and adapter were exactly centered onto the car.
A recent check showed that the adapter is still in place, surviving hot Alabama summers, and performing well 10 years after it was installed.
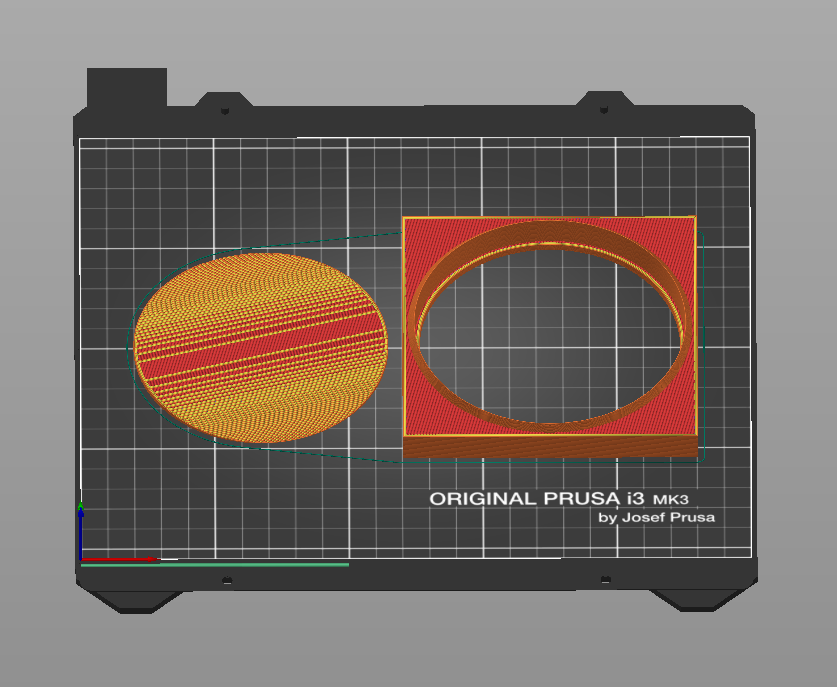
*If you are removing stock emblems or trying to clean up the remaining adhesive residue, use 3M Auto Adhesive Remover.
The most recent project in this genre we’ve tackled was to duplicate a hard-to-find mid-1960s Dodge trim clips for a customer’s restoration project.
There area couple things to take into consideration if you are attempting this yourself:
- If you are printing parts for cars, you probably do not want to make them out of PLA. It will not withstand the hottest outdoor temperatures of most locations and definitely will soften and deform at the internal temperatures that cars will develop on hot days. It’s glass transition temperature is 60C/140F at which point it will start to droop and warp, ruining the part.
- PET-G might be a good midpoint between PLA (cheap, easy to print) and ABS (more expensive, higher temperature tolerance, difficult to print.) PET-G has higher temperature (glass transition is 85C/185F), prints easily, doesn’t give off toxic fumes and is affordable.
- for temperature stability, the best material to make car parts out of is probably ABS. ABS’ glass transition temperature is 105C/221F, which, while not indestructible, will stand up to most interior and exterior temperatures a car will experience (engine bay and exhaust temperatures will go much higher than that.) ABS does need proper ventilation while printing as it gives off toxic fumes while it is printing.
- You’ll also want to consider UV resilience on exterior parts, flexibility/rigidity, impact resistance, vibration dampening and other plastic traits in your design.
- we do not design parts that are directly safety-related, mechanical in nature, or that work around engine bay or exhaust heat. If you are working with extremely high temperatures, plastic is not the material you are looking for.
If you are looking to have a rare part duplicated or a custom part designed please feel free to reach out to us with your requirements for a quotation. We’d be glad to design and draft your part and can print your parts as well. We can also do print-on-demand if you